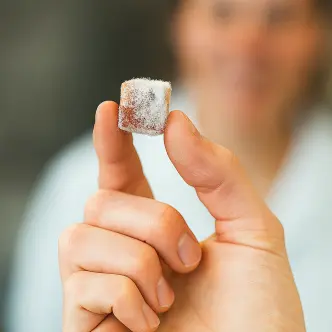
From ingredients to finished product
Gums and jellies come in a variety of shapes, colours and flavors. There are all kinds of different machines involved in making a gum or jelly. The process consists of six different steps. At Tsnis we offer all the machinery you need to produce your unique product. These machines include the preparation, cooking, blending, depositing, conditioning and finishing of your product. But what exactly does the process of raw materials to final candy product look like?
The kitchen
The first step of raw material to the final product is making premix. Premix usually consists of sugar, glucose, water and gelatine or pectin. It is made by first weighing the ingredients, adding them into the vessel and then mixing them. When this is done, the premix will be pumped or transported by vacuum to the next stage of the process; cooking.
Cooking premix is step two of the process to make a gummy. During the cooking the premix is pumped through a stainless steel heat exchanger. The premix will turn into a clear solution.
Next up is blending; adding additives such as colour and flavor to the cooked mass. This is also the step where you can add active substances like CBD to the candy. The weighing, cooking and blending machines form ‘the kitchen’. OTC Candy is a specialist when it comes to accurately measuring active ingredients such as CBD in candy as well as masking odors and flavors. This is important to understand when you are orientating yourself on buying CBD gummy manufacturing equipment.
Moulding and Demoulding
After the raw materials have gone through the first phase of the candy manufacturing equipment and have formed a final candy mass, the moulding can start. During step four, the depositor can turn the candy mass into all sorts of fun and fancy shapes. After conditioning of the product, OTC Candy is also able to supply an automatic demoulding system. This makes the labor intensive work of manual demoulding unnecessary.
Conditioning
Conditioning rooms contain air handlers which have several functions: filtering, cooling, heating, blowing and air compression. This delivers an airflow across the room that causes the gummies to dry and form to your final conditioned product.
Finishing
Last but not least; the finishing of the gummies. After conditioning the candy in the conditioning room and demoulding of the candy, the candy will get its final touch with the De-Oiler and optionally the Sugar Sander. The De-Oiling drum will automatically remove any excess oil of the gummies while the Sugar Sander is a fully automatic system for continuously controlled sugar coating of soft boiled gummies.
Tanis OTC equipment
Nutraceutical gummies require a very specific balance that maintains active ingredient efficacy, ensures accurate dosing, masks unpleasant flavors and avoids cross-contamination.
Tanis production lines have been perfected to deliver all of this.
The Tanis OTC non-starch production lines are precision-engineered to suit the demand for gums and jellies enriched with active ingredients. Starchless machinery facilitates cleaner ingredient profiles, aligning with the trend towards more natural and transparent product labeling in the confectionery industry. Moreover, it guarantees no cross-contamination, ensuring the purity of the final products and enhancing overall efficiency in gums and jellies production.
400S, equipment that helps you grow organically
In addition to this, a unique scalable solution with the Tanis 400S is offered, allowing startups to enter the world of automated confectionery & nutraceutical manufacturing. By gradually investing in the individual parts, the production line grows along with the company.
If you are interested in our manufacturing equipment, take a look at our machinery page or contact us!
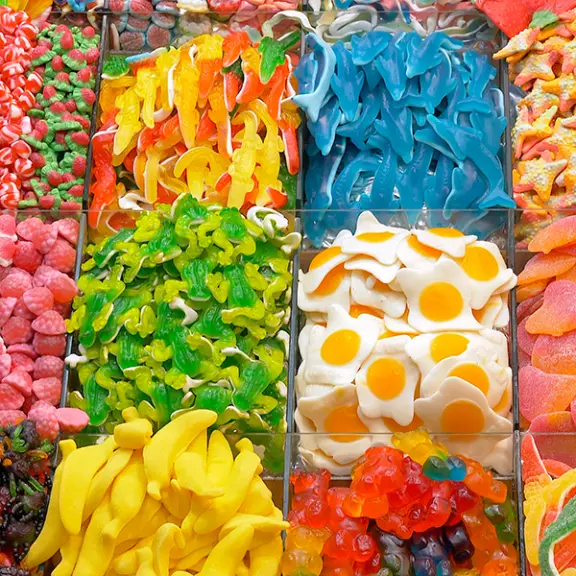