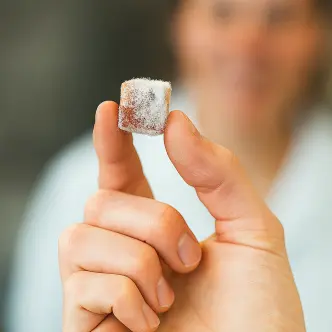
For over 5 Years of Pioneering: Tanis' Compact Lines with Gantry Feeder and Stacker Solution
At Tanis, we're committed to pushing the boundaries of candy production efficiency and quality. For over 5 years, we've been utilizing the Gantry Feeder and Stacker solution in our fully automated compact starch or non-starch moulding lines, reducing downtime due to chain transport massively. This range of moguls is designed to keep things simple, combining modern servo technology for smooth flow through the moulding line with robust walking beam movements. Since the first successful commissioned project in 2018, we have been perfecting our Gantry systems and are proud as entrepreneurs to include our fifth generation Gantry Feeder and Stacker in our portfolio.
Tanis moulding lines, how does it work?
Pallets, with stacks of trays, can be placed into the infeed of the moulding line using a pallet truck. Depending on the chosen options, the pallets are buffered, and the stacks of trays are unloaded from the pallet into the system.
The trays are singled out and placed onto the moulding line by means of a walking beam. The tray then moves through the moulding line, entering the starch buck where the tray is flipped over, and candy and starch fall onto the sieve where the starch is separated from the candy pieces in a process called demoulding. The candy pieces are then dropped onto a conveyor and leave the moulding line, while the starch is recirculated back to the infeed of the starch filler.
Once demoulded, the tray is upright again and filled with starch, with a static plow evening out the starch. The tray is now ready to be “printed”, where a mouldboard pushes the candy models into the starch, leaving a perfect imprint.
The tray is then ready to leave the starch buck. Depending on the chosen options, a print check can be done by a vision camera, which checks for imperfections in the starch imprint and any leftover candy mass or pieces.
Why Gantry Robots Instead of Chains?
Our Compact moulding system utilizes a Gantry robot for infeed and outfeed instead of chains. This choice reduces the number of moving parts, decreases wear and tear, and utilizes servo-driven mechanisms. Unlike chains, Gantry robots eliminate the need for alignment adjustments, as uneven wear of individual chains can be an issue. Additionally, our moulding system features one large walking beam, resulting in fewer components and less fine-tuning.
Moreover, our compact moulding lines with the Gantry Feeder and Stacker solution are also well-suited for replacing aging moulding lines. Their compact size and compatibility with existing infrastructure make them an ideal choice for upgrading production capabilities without the need for a complete overhaul.
In conclusion, our compact lines with this technology have revolutionized our candy production processes, providing us with the technical reliability and performance needed to stay ahead in a competitive market. If you're looking to optimize your production capabilities or replace your moulding line, consider integrating this proven, but innovative technology into your operations.
For more information on how our compact lines can benefit your candy manufacturing processes, contact us here.
Our Starch and Non-starch solutions with Gantry system in real life?
During the Tanis Gummy Summit, we will present both a Starch and Non-Starch moulding line equipped with our latest generation Gantry System. On May 22 and 23, partners from all over the world will join us during this informative event at our headquarters in Oosterhout, the Netherlands. Follow us and stay tuned to step into the innovative world of Tanis next time as well.
Click here to learn more about our Compact Production Lines
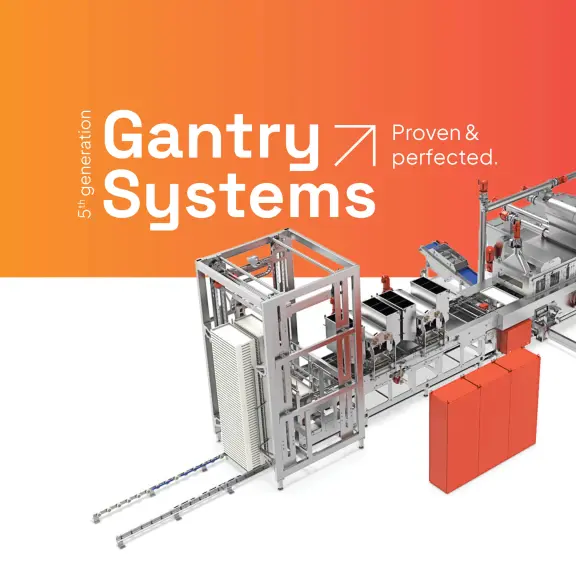